Inventory / To Die For
The bamboo hoops of Matthew Lewandowski
Marc Ganzglass
“Inventory” is a column that examines or presents a list, catalogue, or register.
Door-knocker earrings are a type of hollow-form jewelry that first became popular in New York in the late 1970s. They are made in gold and silver and come in a broad array of finishes and styles, including hearts, stars, trapezoids, kissing dolphins, and Nefertiti heads. The most popular, however, are bamboo hoops.
Today, you can still find bamboo hoops in jewelry shops and department stores around the city, and for sale on television channels such as the Home Shopping Network and QVC. The earrings are manufactured in small factories and sold by the pound to jewelry wholesalers, who resell them to retailers, street vendors, and larger chain stores. Unlike fashion apparel, in which new designs are developed for each season, designs in the wholesale jewelry market are constantly evolving, driven as much by the cost of gold and silver as they are by consumers’ tastes.
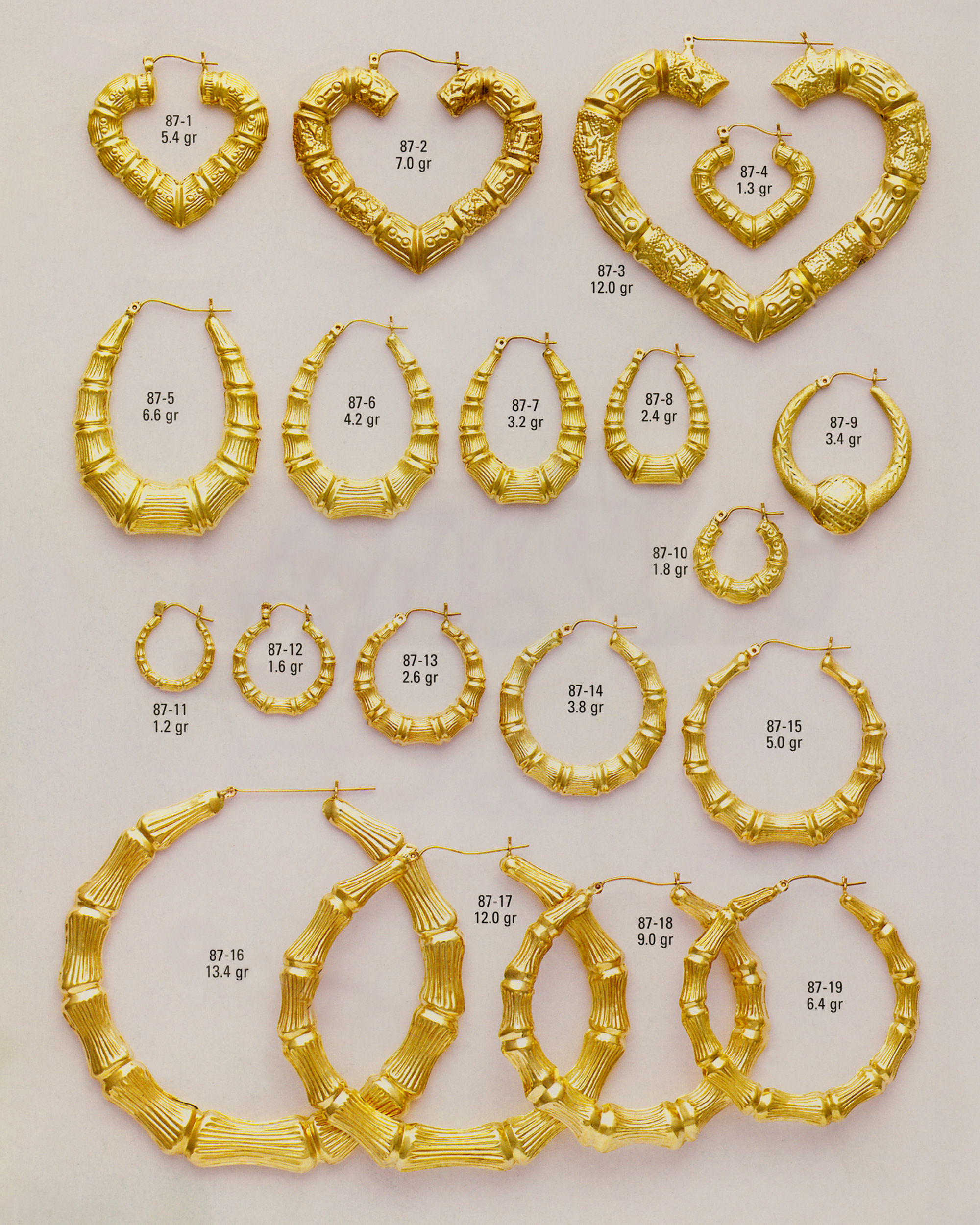
Hollow-form jewelry is made by stamping very thin gold or silver sheet metal into two symmetrical shells that are then soldered together to create a volumetric form, giving it the appearance of expensive solid gold jewelry but at a fraction of the cost. This technique, as well as its use in mass production, dates back to the beginning of the Industrial Revolution and the development of high-speed punch presses that could stamp out large quantities of parts with great precision. The manufacturing process led to a whole new class of consumer goods that approximated high-style luxury items, even as the ease and speed of production allowed for popular imagery to be quickly incorporated into their designs. The job of rendering the panoply of forms fell on the shoulders of the tool- and diemaker. Part sculptor, part technician, the tool- and diemaker was responsible for turning each new design into an accurate three-dimensional engraving that could be used to stamp out as many units as the market could bear.
The process begins with a design on paper. The toolmaker translates this sketch into a working drawing describing the exact shape, profile, and elevation of the piece. The working drawing is transferred to a block of steel, which is then carved by hand into a three-dimensional form, after which fine details are engraved into the surface. The steel block is then hardened; this is the master model called a hub. Next, the hub is pushed into a heated steel block using a hydraulic press. This negative image of the hub is called the die. With the die completed, the toolmaker pushes yet another block of steel into the negative form to produce a second master model called a forcer—the positive form used in the actual stamping of the jewelry. The pair of forcer and die is called a die-set and is sent to the manufacturer for use in production. The original hub is kept by the toolmaker in case the die-set needs to be replaced.
Many of the bamboo hoops sold in New York were made from die-sets produced at Matthew Tool and Die Co., a small machine shop in Brooklyn founded by a Polish immigrant named Matthew Lewandowski. Originally trained as an economist in Poland during the communist regime, Lewandowski began tool- and diemaking as a second career when he and his family emigrated to New York in the early 1970s. On the following pages are images of just a few of the nearly ten thousand hubs made by Lewandowski between 1978 and 2011; all of those pictured here were used to make bamboo hoops, though Matthew Tool and Die Co. produced die-sets for a wide variety of earrings, bracelets, and charms.
Figure 1 is an early example of a bamboo hoop from the 1970s. It is relatively small, about 1 3/8 inches across. As bamboo hoops became more popular, manufacturers demanded larger and larger versions while stamping the shells out of increasingly thinner material. When Lewandowski opened his shop in 1978, he was making dies for stamping ten-karat gold six-thousandths of an inch thick; by the mid-1980s, it was half that, just three-thousandths of an inch thick for a three-inch-wide bamboo hoop. These incredibly thin shells easily dented and crumpled, and the failure of the metal was so common that women often flattened the earrings themselves as soon as they bought them.
Figures 2, 3, and 4 are examples of the extremely large bamboo hoops that were popular in the early 1980s. Because different wholesalers offered nearly identical products and because Lewandowski supplied production tools to competing manufacturers, he made the ethical decision early on never to give identical tools to different clients. Rather, he would recreate the hubs from scratch each time, resulting in the slight differences seen in these three hoops, which range in size from 2 3/4 inches to 3 1/2 inches in diameter.
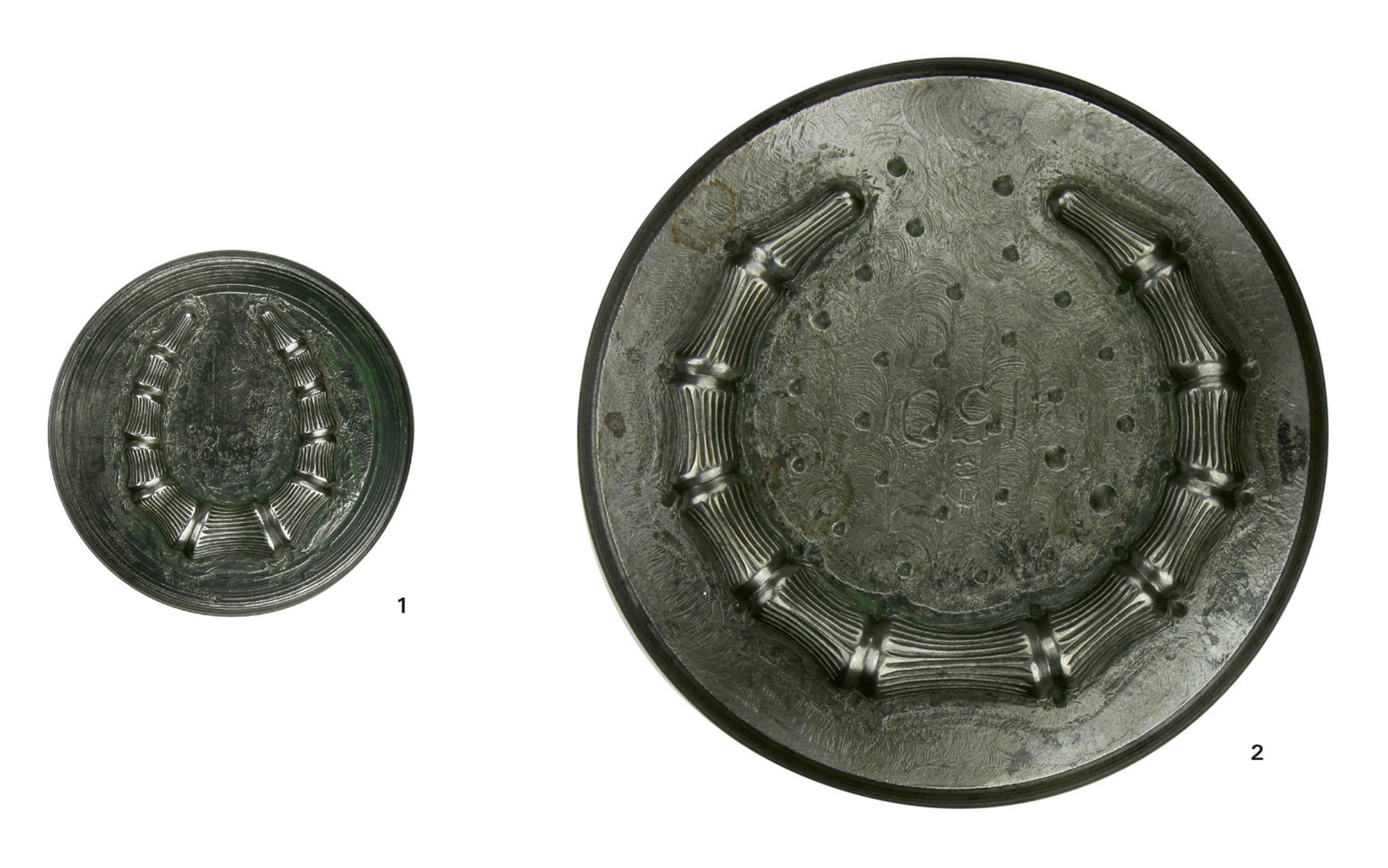
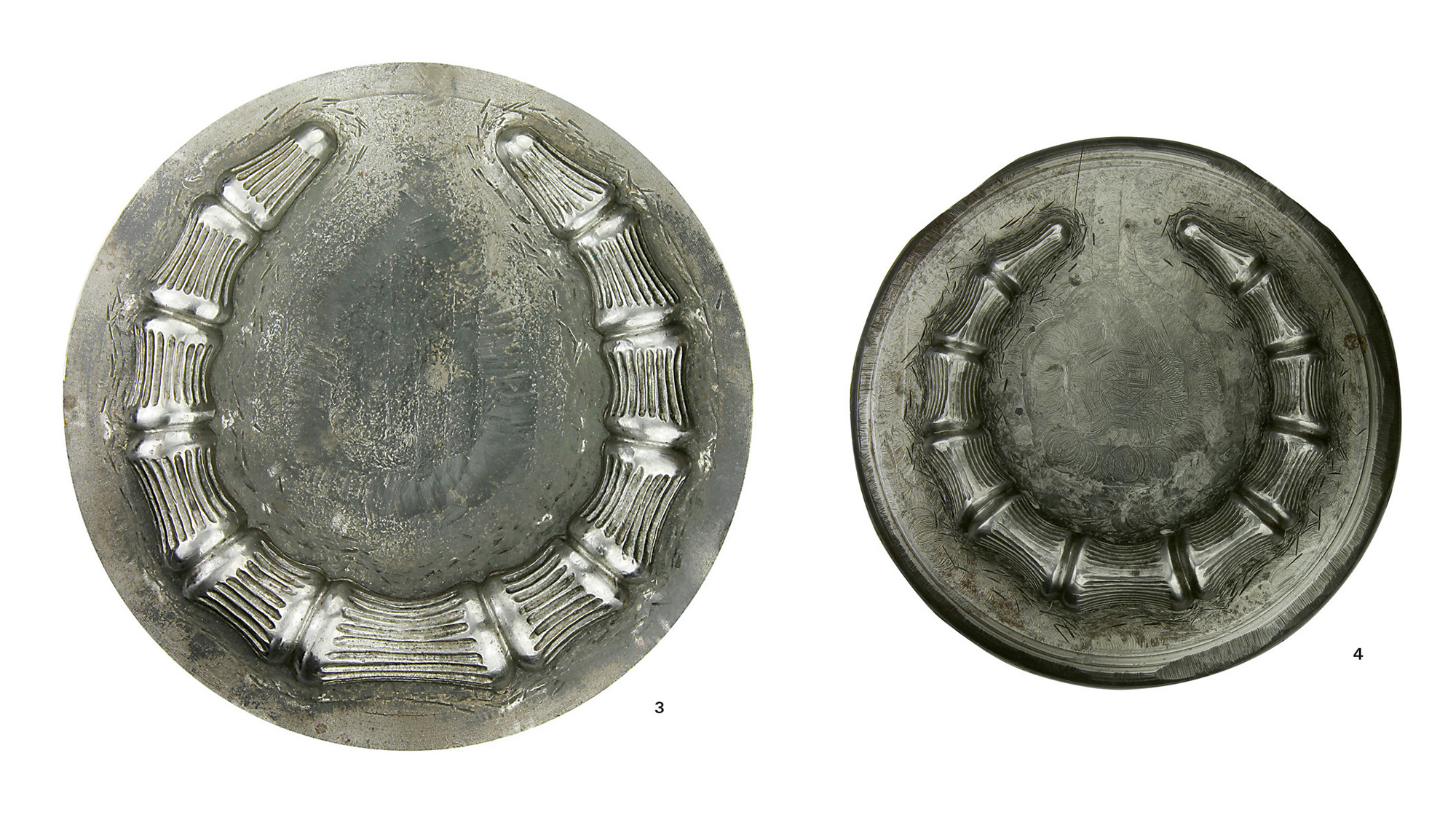
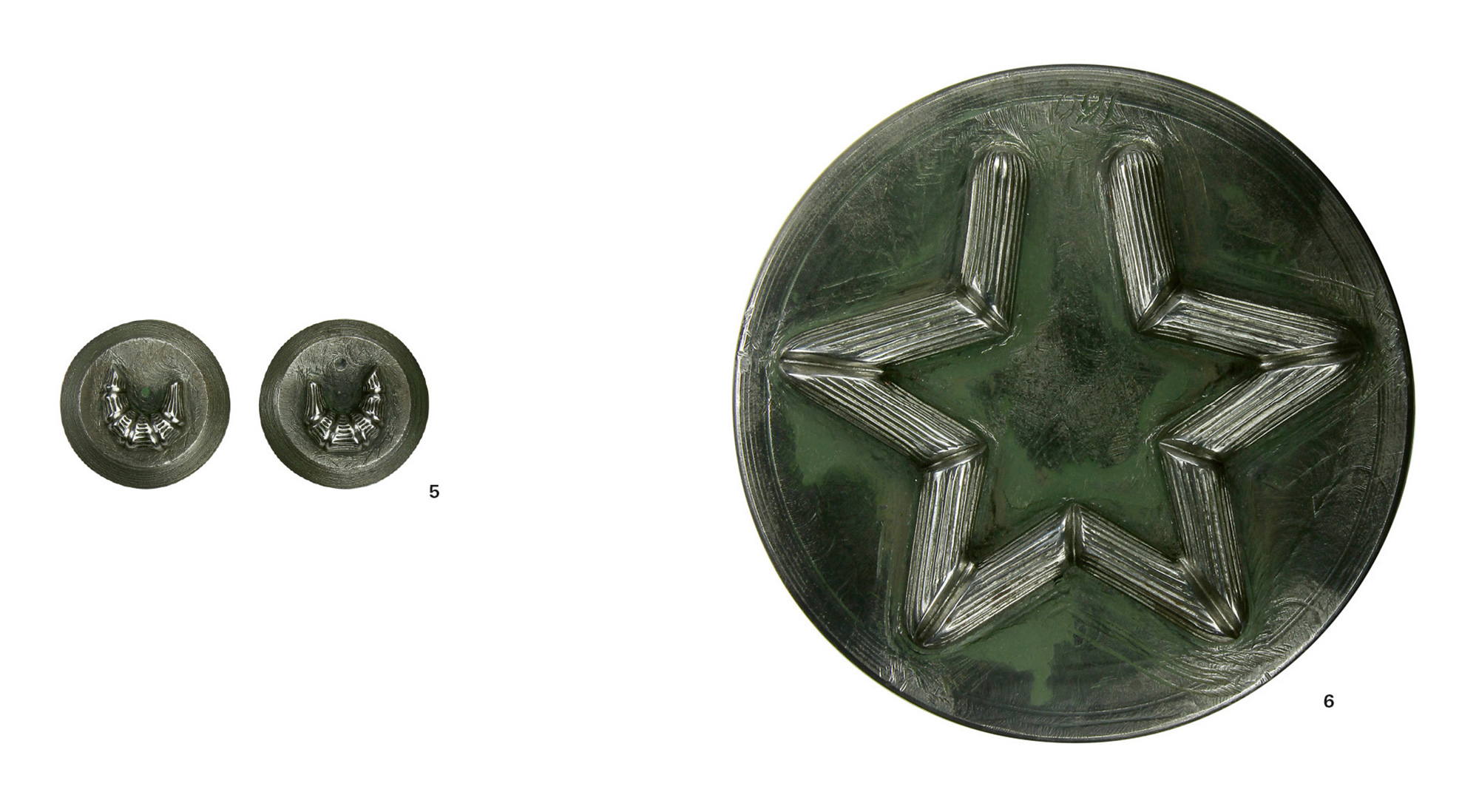
Sometimes earring designs were modified extemporaneously, either with the manufacturer requesting something over the phone or because Lewandowski was trying out a new idea. In part because of the speed with which these tools were being produced, no detailed records exist of who initiated these changes in design. Within a specific style, there could be countless variations and this is especially evident in the morphology of the bamboo hoops.
In the pair of mini-hoops in figure 5, the bamboo is rendered in the same naturalistic style as the larger models, but the hoops are so compressed that the motif is almost lost. These hubs are also a good example of one of the technical idiosyncracies of stamping hollow-form jewelry. Any design that is symmetrical along its central axis only requires one hub, as seen in the classic bamboo hoop. But designs asymmetrical along their central axis—such as these smaller earrings—require two mirrored hubs. If the design calls for asymmetrical patterns that are different for each ear, four hubs would be needed.
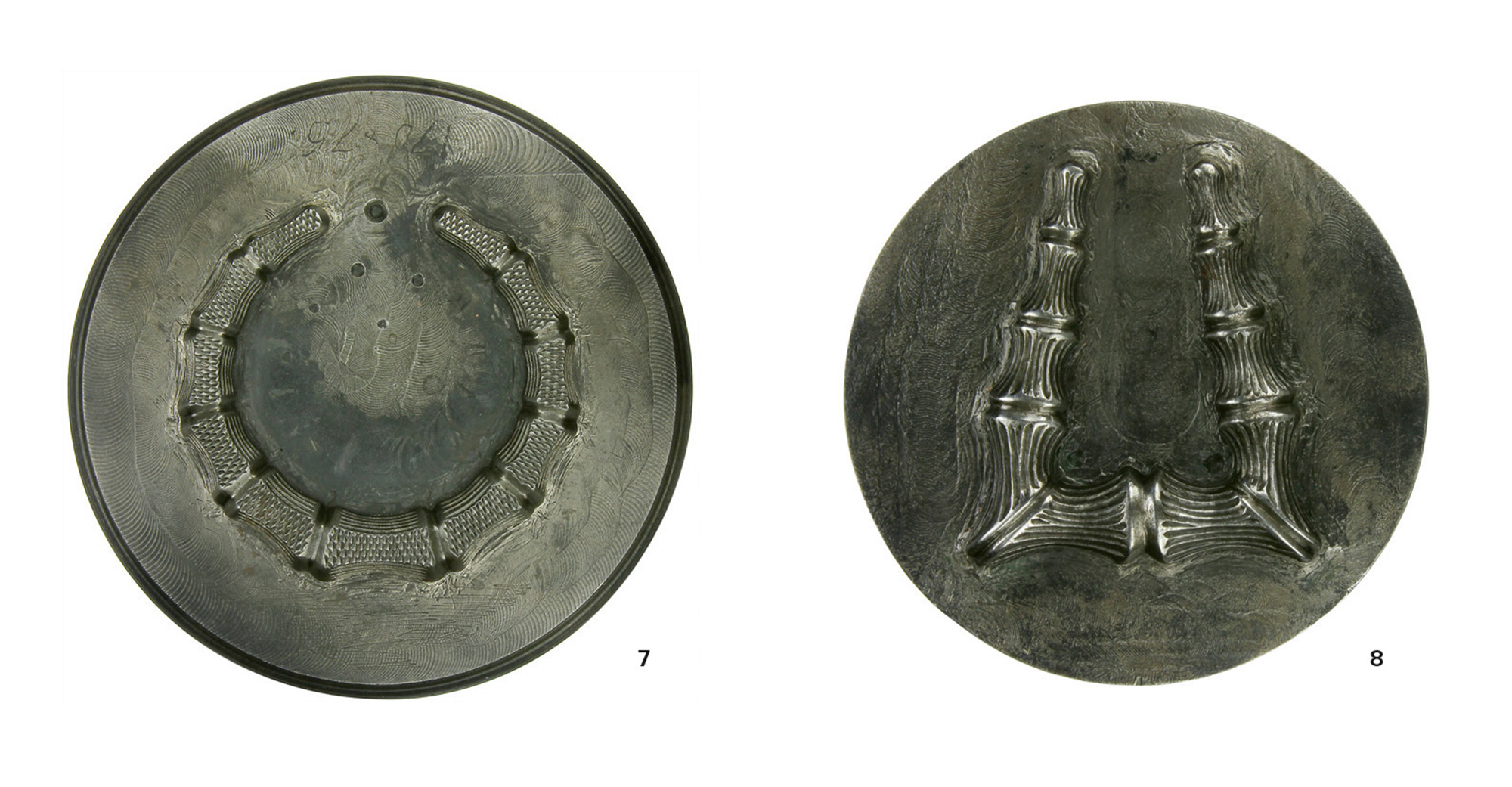
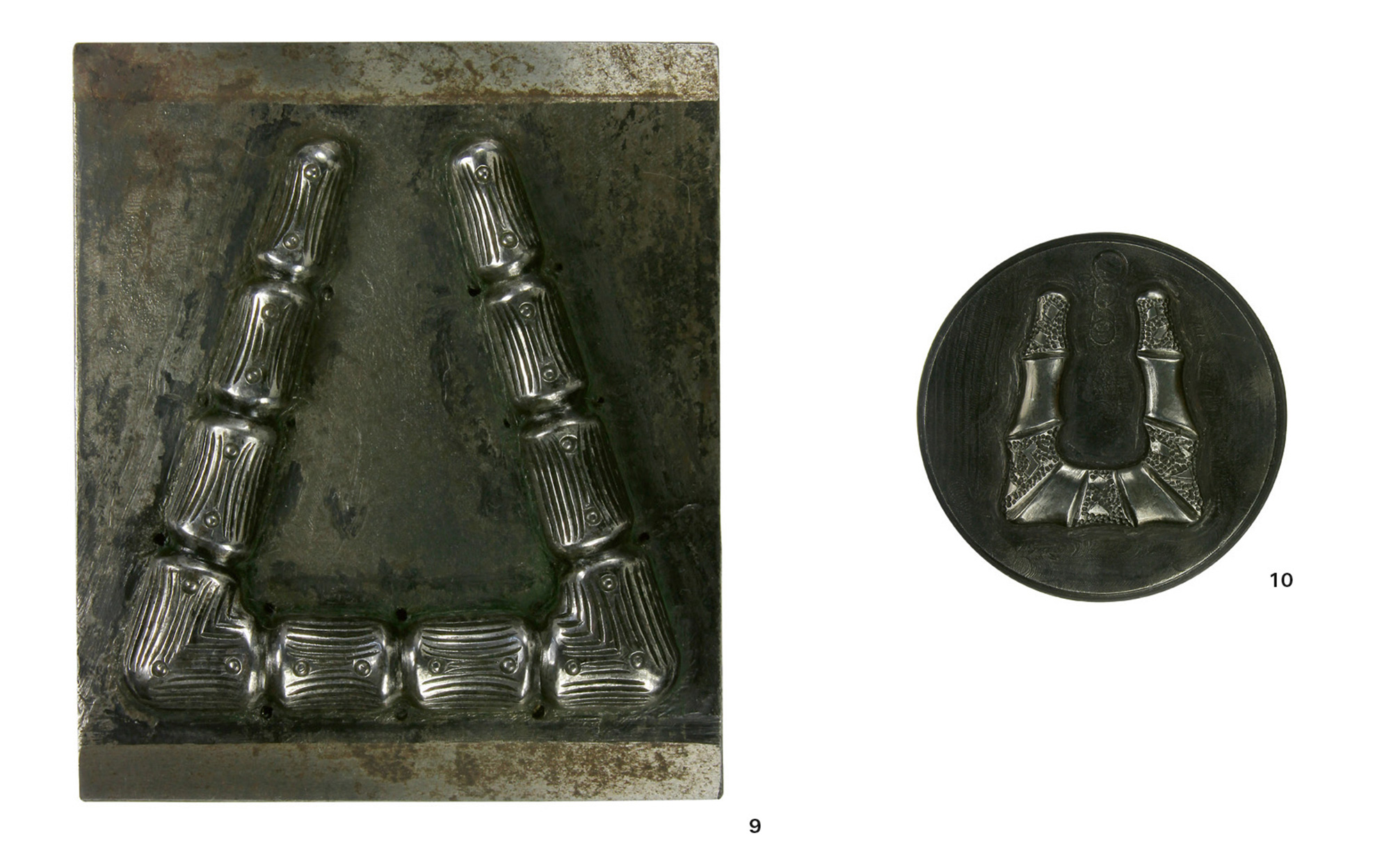
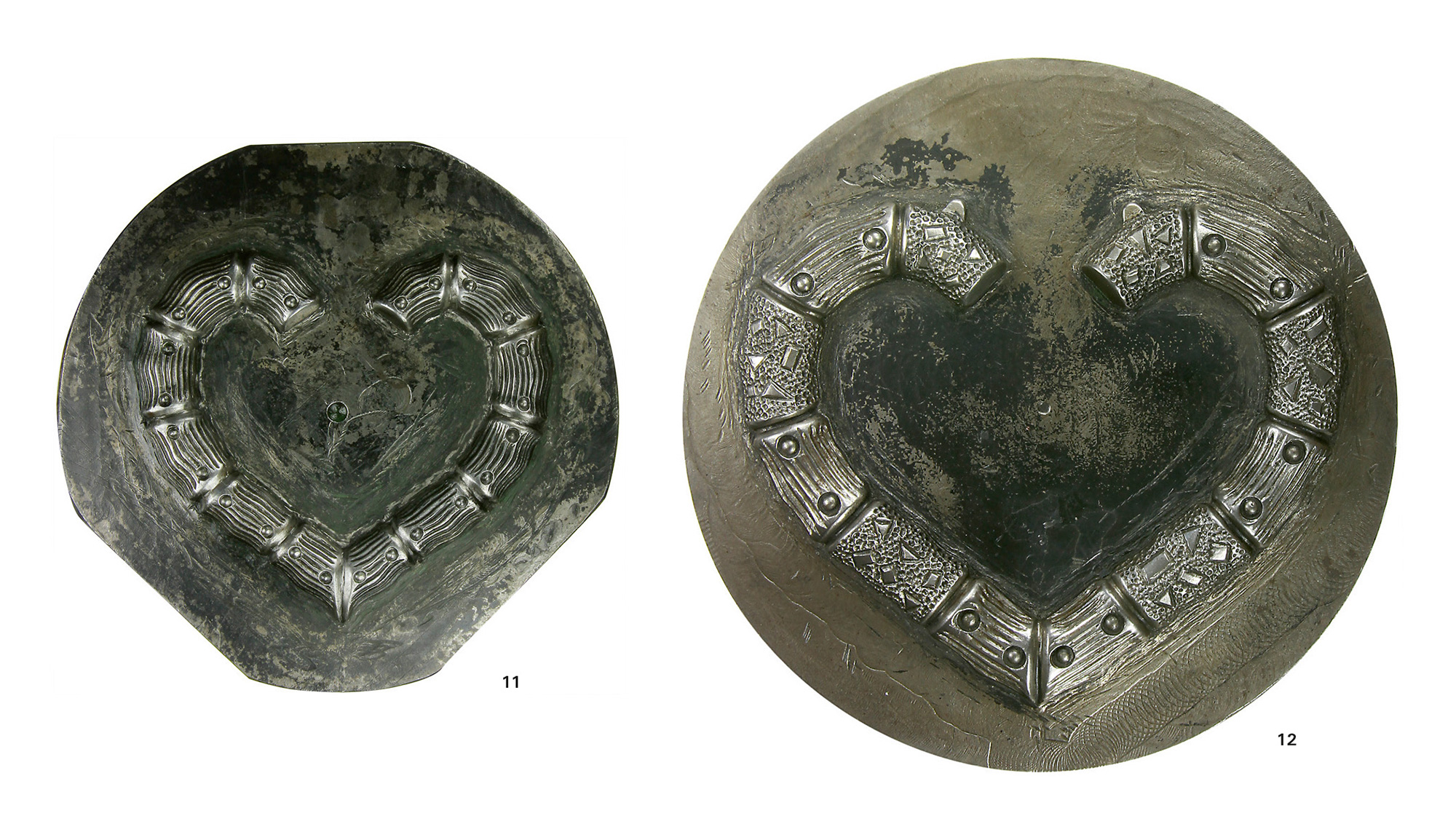
The hub in figure 6 deviates from the hoop form altogether. In this star-shaped earring, the bamboo motif is abbreviated—the segments are straight and the joints are mitered. The vocabulary changes again in figure 7. Its segmented shape and detailing along the sides are definitely bamboo-like, but the cross-hatching on the top surface approximates the type of knurling found on machinery handles.
While the trapezoidal hoops in figures 8 and 9 appear similar, there is an important modification. In figure 8, the bamboo segments are rendered in the standard way, while in figure 9 they appear to be held together with rivets. This is an illustration of a construction detail typically used for fastening sheet metal, not bamboo. Another notable departure can be seen in figures 11 and 12. Rivets again appear in these heart-shaped hoops, but in figure 12 the bamboo segments alternate with segments composed of geometric nuggets on a field of stippling. This type of detail is reminiscent of repoussé panels found on traditional metal hollowware, such as Stickley-style copper vessels. In figure 10, the bamboo has all but disappeared, and the hub is composed only of alternating smooth and nugget-infill segments.
Because of the lack of detailed records, it is hard to chart how and under what conditions the bamboo hoop changed over time. The production of tooling for the wholesale jewelry market was fast-paced and fluid, with designs evolving at multiple levels of production simultaneously. In these circumstances, the toolmaker was afforded exceptional latitude when it came to rendering forms for production—a latitude that is clearly evident in this selection of hubs by Matthew Lewandowski.
Marc Ganzglass is an artist based in Brooklyn. In 2011, he opened Space for Art and Industry, a non-profit gallery at the Brooklyn Navy Yard. He is currently a visiting assistant professor of sculpture at Virginia Commonwealth University.